© 2025 Fusion Inc. All Rights Reserved. | Optimized by Actual SEO Media | Sitemap
If you are curious about Houston TX Metal Spray Coating Services, then you have come to the right place. At Fusion Inc., we place a high value on the benefits of our service and everything they can do for your business projects. We know that our results will never disappoint you. With over 100 years of experience, young innovative minds, and incredible efficiency on our side, our precision is above the standards set in any industry. Your equipment will function far better and last for much longer when you provide it with one of our coatings.
If you are new to the concept of spray coating, you may be a bit lost. In order to fully understand what a spray coating is and what all of the options it carries, we have created this article for your convenience. Our goal is to increase your awareness of our services by providing you with accurate and comprehensive information so you feel more confident when on the market.
As for those who may already have potential interests in our services, this article should be a great indication that we have all of the skills and equipment that you might need. We are highlighting the different types of metal spray coatings and describe the processes they take and the benefits you’ll receive as a result. Fusion has been a leading brand for rotational and reciprocating component repairs since 1959 and we don’t want to let up now.
Different Kinds Of Houston TX Metal Spray Coating Services
Thermal spray coating is a method which many industries utilize. Fusion happens to offer some of the highest quality spray coatings in Houston. Our spray processes are very thorough and efficient. Through the use of molten powdered materials that are applied with heat, electricity, plasma or compressed air, we can coat your equipment in a protective layer that will make it more resistant to some of the factors that could contribute to its degradation.
These coatings are assisting business-owners all over the world by increasing the lifetime and operational efficiency of their products. You can see coatings being applied to units such as airplanes, buildings, oil drill bits, and other industrial equipment. Their resistance to elements, heat, and friction are outstanding and certainly worth the effort.
Plasma Spraying
This method employs a plasma torch and specific powders for coating. By superheating the gases between the cathode and the anode (nozzle & electrode) of the torch, we are able to generate an incredibly hot plume of plasma. It will reach heats in excess of 12,000 degrees Fahrenheit with the potential to reach 30,000 degrees Fahrenheit if the proper circumstances are present.
A metal or ceramic powder is then administered into the plasma current at a regulated rate. The powder, which can be made of metal alloys, ceramics, cermet, carbides and more. At this point, the powder is immediately melted down once it reaches the plasma and is projected out of the nozzle at a precise magnitude that performs excellent coatings with high bonding rates.
This particular method is excellent for very complex geometries. It will also be great if you want to apply a very controlled and isolated coat. Our equipment provides the ability to coordinate the thickness and porous levels of the coating. With the proper robotics in place, this entire process can be automated if we wish it.
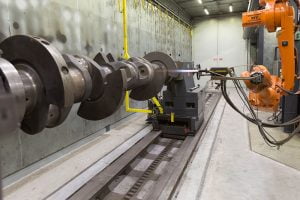
We work with large scale components for all types of industries
Combustion Flame Spraying
If you are attempting to coat a surface to withstand great amounts of stress, this process would be ideal. For this process, we will generate a flame through the use of oxygen and acetylene. The result creates a very hot flame that then melts the metal alloys or pure metals into droplets. At that point, compressed air will push the droplets at a controlled rate onto the substrate.
HVOF (High-Velocity Oxy-Fuel Spraying)
For a coating that is one of the most resilient, turn your attention toward our HVOF coatings. This process utilizes an oxygen-fuel mixture that applies generates a very strong flame evenly to the surface. By the rapid particle acceleration, the coating mixture is applied with an incredible force of 3,200 feet per second.
The bonds that these coats exhibit are so strong that they are capable of exceeding 12,000 PSI. You will find that this low porous option can produce minimal oxides and extremely fine particle distribution for manufacturers that want to have a smooth finish to their products.
Coating materials we use are as result very dense, this type of method is going used most often for dimensional restoration repairs or corrosion control as they have incredible resistance to the corrosion levels many industries experience. We use mostly superalloys and carbides as the material for coating, and it really makes a difference. Most other industrial coats cannot handle the degree of corrosion our coats can. In fact, many OEMs will use an HVOF thermal spray coating to extend the lifetime of their products.
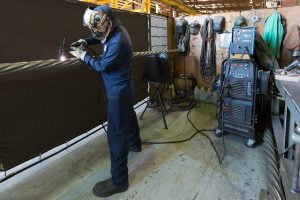
Our team works around the clock to get you the best results!
Twin Arc Spraying
This process is a bit more complex than some of the methods above. As the name implies, this type utilizes an arc gun that holds two conductive wires. Then these wires are fed through the gun. They are electrically charged to super high temperatures. When there is a connection between the two wires, they will begin to melt.
This method is somewhat similar to combustive spray coating, but instead of using a torch, we only use compressed air to push the atomized particles of the wires onto the substrate. The wires will usually be aluminum or zinc. Through the method of Twin arc spraying, the equipment can self-contain the metal coating. It does not distort the components with heat and produces high spray rates for productivity.
The Benefits of Spray Coating
Spray coating is, simply put, a method which allows components to resist damage from heat and erosion. At the same time, you can increase its use and longevity as well. This means that your equipment will perform more efficiently for longer durations. As someone with a mind for business, we understand that you would prefer for your products to work for as long as possible before needing replacements. Fusion has you covered!
Thermal spray coatings such as the ones we mentioned today can be your answer to heat resistance, cold resistance, weather erosion, and friction damage. The personnel at Fusion Inc. are highly qualified to handle all of your thermal spray coating needs. Whatever the nature of the project, we can improve your success rates by applying our coatings.
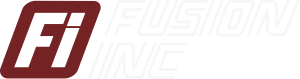
Thermal spray coating services available now!
Contact Us
In order to get in touch with us about thermal spray coating, call us at (713) 691-6547. At Fusion, we want to provide you with the best results for thermal spray coating. We hope that this article increased your understanding of what we do at Fusion. At Fusion Inc., we have many machine capabilities which are listed and outlined for your convenience here. Our company can provide you with the best Houston TX Metal Spray Coating Services.
Fun Facts About Houston
- The namesake of Houston, Sam Houston, was an honorary member of the Cherokee nation.
- While Austin may be the capital city now, Houston was the capital city of Texas from 1837 to 1839.
- Our Texas Medical Center sees over 7.2 million patients each year. Those numbers are huge!
- To learn more about Houston, click here!
If you are curious about Houston TX Metal Spray Coating Services, then you have come to the right place. At Fusion Inc., we place a high value on the benefits of our service and everything they can do for your business projects. We know that our results will never disappoint you. With over 100 years of experience, young innovative minds, and incredible efficiency on our side, our precision is above the standards set in any industry. Your equipment will function far better and last for much longer when you provide it with one of our coatings.
If you are new to the concept of spray coating, you may be a bit lost. In order to fully understand what a spray coating is and what all of the options it carries, we have created this article for your convenience. Our goal is to increase your awareness of our services by providing you with accurate and comprehensive information so you feel more confident when on the market.
As for those who may already have potential interests in our services, this article should be a great indication that we have all of the skills and equipment that you might need. We are highlighting the different types of metal spray coatings and describe the processes they take and the benefits you’ll receive as a result. Fusion has been a leading brand for rotational and reciprocating component repairs since 1959 and we don’t want to let up now.
Different Kinds Of Houston TX Metal Spray Coating Services
Thermal spray coating is a method which many industries utilize. Fusion happens to offer some of the highest quality spray coatings in Houston. Our spray processes are very thorough and efficient. Through the use of molten powdered materials that are applied with heat, electricity, plasma or compressed air, we can coat your equipment in a protective layer that will make it more resistant to some of the factors that could contribute to its degradation.
These coatings are assisting business-owners all over the world by increasing the lifetime and operational efficiency of their products. You can see coatings being applied to units such as airplanes, buildings, oil drill bits, and other industrial equipment. Their resistance to elements, heat, and friction are outstanding and certainly worth the effort.
Plasma Spraying
This method employs a plasma torch and specific powders for coating. By superheating the gases between the cathode and the anode (nozzle & electrode) of the torch, we are able to generate an incredibly hot plume of plasma. It will reach heats in excess of 12,000 degrees Fahrenheit with the potential to reach 30,000 degrees Fahrenheit if the proper circumstances are present.
A metal or ceramic powder is then administered into the plasma current at a regulated rate. The powder, which can be made of metal alloys, ceramics, cermet, carbides and more. At this point, the powder is immediately melted down once it reaches the plasma and is projected out of the nozzle at a precise magnitude that performs excellent coatings with high bonding rates.
This particular method is excellent for very complex geometries. It will also be great if you want to apply a very controlled and isolated coat. Our equipment provides the ability to coordinate the thickness and porous levels of the coating. With the proper robotics in place, this entire process can be automated if we wish it.
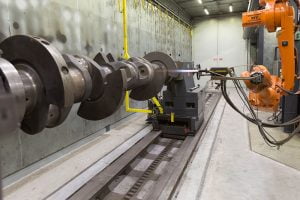
We work with large scale components for all types of industries
Combustion Flame Spraying
If you are attempting to coat a surface to withstand great amounts of stress, this process would be ideal. For this process, we will generate a flame through the use of oxygen and acetylene. The result creates a very hot flame that then melts the metal alloys or pure metals into droplets. At that point, compressed air will push the droplets at a controlled rate onto the substrate.
HVOF (High-Velocity Oxy-Fuel Spraying)
For a coating that is one of the most resilient, turn your attention toward our HVOF coatings. This process utilizes an oxygen-fuel mixture that applies generates a very strong flame evenly to the surface. By the rapid particle acceleration, the coating mixture is applied with an incredible force of 3,200 feet per second.
The bonds that these coats exhibit are so strong that they are capable of exceeding 12,000 PSI. You will find that this low porous option can produce minimal oxides and extremely fine particle distribution for manufacturers that want to have a smooth finish to their products.
Coating materials we use are as result very dense, this type of method is going used most often for dimensional restoration repairs or corrosion control as they have incredible resistance to the corrosion levels many industries experience. We use mostly superalloys and carbides as the material for coating, and it really makes a difference. Most other industrial coats cannot handle the degree of corrosion our coats can. In fact, many OEMs will use an HVOF thermal spray coating to extend the lifetime of their products.
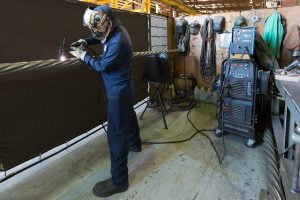
Our team works around the clock to get you the best results!
Twin Arc Spraying
This process is a bit more complex than some of the methods above. As the name implies, this type utilizes an arc gun that holds two conductive wires. Then these wires are fed through the gun. They are electrically charged to super high temperatures. When there is a connection between the two wires, they will begin to melt.
This method is somewhat similar to combustive spray coating, but instead of using a torch, we only use compressed air to push the atomized particles of the wires onto the substrate. The wires will usually be aluminum or zinc. Through the method of Twin arc spraying, the equipment can self-contain the metal coating. It does not distort the components with heat and produces high spray rates for productivity.
The Benefits of Spray Coating
Spray coating is, simply put, a method which allows components to resist damage from heat and erosion. At the same time, you can increase its use and longevity as well. This means that your equipment will perform more efficiently for longer durations. As someone with a mind for business, we understand that you would prefer for your products to work for as long as possible before needing replacements. Fusion has you covered!
Thermal spray coatings such as the ones we mentioned today can be your answer to heat resistance, cold resistance, weather erosion, and friction damage. The personnel at Fusion Inc. are highly qualified to handle all of your thermal spray coating needs. Whatever the nature of the project, we can improve your success rates by applying our coatings.
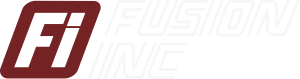
Thermal spray coating services available now!
Contact Us
In order to get in touch with us about thermal spray coating, call us at (713) 691-6547. At Fusion, we want to provide you with the best results for thermal spray coating. We hope that this article increased your understanding of what we do at Fusion. At Fusion Inc., we have many machine capabilities which are listed and outlined for your convenience here. Our company can provide you with the best Houston TX Metal Spray Coating Services.
Fun Facts About Houston
- The namesake of Houston, Sam Houston, was an honorary member of the Cherokee nation.
- While Austin may be the capital city now, Houston was the capital city of Texas from 1837 to 1839.
- Our Texas Medical Center sees over 7.2 million patients each year. Those numbers are huge!
- To learn more about Houston, click here!